1. Filter paper machine to produce filter cartridges pleats.
Putting quality tested filtration media with suitable width on a roller, pleating machine starts making some plates as trial running to adjust pleating speed and pleating height. Pleated design increased the filtration area for deep filtration.
The cutter of the pleating machine set to cut off a certain length of pleated membrane. One worker will gather the pleated membrane into a box and forward to the next procedure. This type of water filter cartridges is available in a wide range of chemical compatibility.
2. Side Seam Thermal Welding
Cutting off cartridge filters the pleats to suit for filter cage
We need to cut off the surplus length on both sides of the thermal welded pleated membrane to make sure it is 20/40/60 inches long to fit the cage and end caps. Length control is important for the filter cartridge integrity. Too long which will affect the flow rate or too short which cause leakage in the filtration process.
Middle seam welder to do seam thermal welding of filter cartridge paper
Ultrasonic thermal welding is a high technology for side seam sealing of membrane pleated, without any additives & glues in the process which making sure 100% integrity of the side seam and not any pollution. Keeping clean and stable for the membrane pleated cartridge filters and high flow pleated filter cartridge in the filtration process.
3. Cartridge shape
Putting the correct length pleated membrane which contains an inner core inside into the outer cage. Assembled Semi-finished filters which placed neatly to clean and tidy box, waiting for the next step.
4. End caps for welding
To welding Flat cap onto both ends of the filter cartridge, which makes pleated membrane, inner core & outer cage together as 100% integrity.
5. Fitting end caps and filter cartridge length connecting welding
Fitting end cap
Putting the end caps on both ends and the filter cartridge in the middle of end caps thermal welding machine.
Setting suitable temperature, Two end caps which could be fin, 222, 215, 226 moves forward to the middle and get in touch with a flat cover.
A few seconds later, end caps, pleated membrane and outer cage & inner cage are thermal welded together to form a complete pleated filter cartridge.
Length connecting
Welding 2/3 pieces together to complete 40/60 inches long high flow pleated filter cartridge, so that all the part of the pleated filter cartridge is thermal welded together, complete the production of membrane pleated cartridge filter.
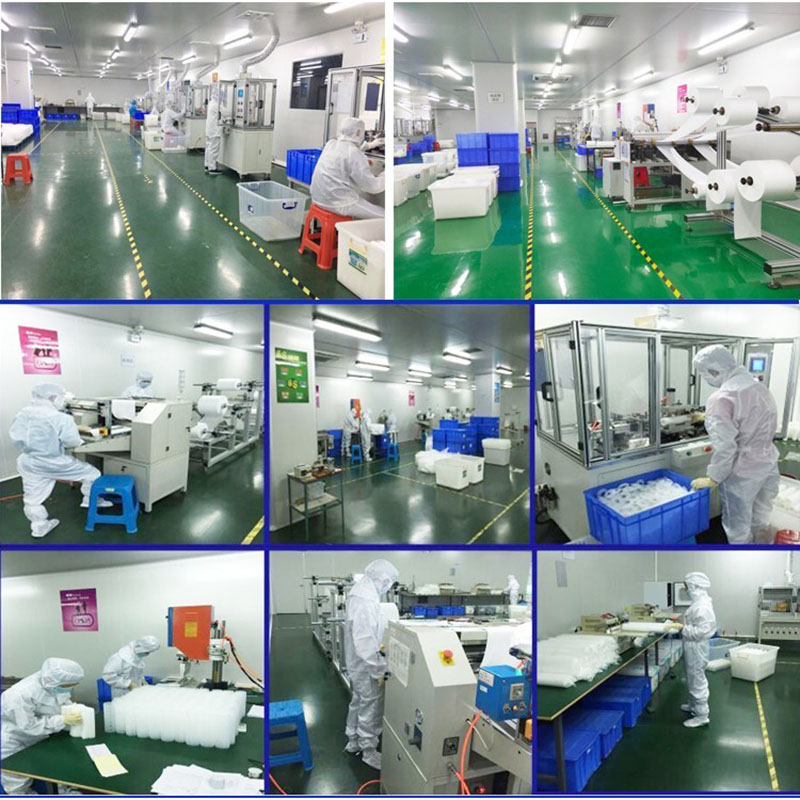
Post time: Mar-06-2021